Automatic Block and Paving Stone Machine
presmakina.com
Automatic Concrete Block Machine Manufacturer
(+90) 326 451 26 66

Tailor-Made Designs That Exceed Expectations
We create unique and aesthetic designs that fully meet the needs and expectations of our clients.
Board Dimension 1400*1100 Board Dimension 1400*1300
PM Series Automatic Concrete Block Making Machines are engineered to deliver high performance, precision, and reliability in block production. With an integrated additional package system, these machines optimize the handling and preparation of concrete blocks, streamlining the entire production process.
PRS 3000 Fully automated concrete block-making machines are designed to deliver unparalleled efficiency and precision in block production. These advanced machines come equipped with an additional package system and integrated curing systems, ensuring optimal quality and production speed.

PM 1411-1200
Board dimensions 1400x1100 mm
DIMENSIONAL FEATURES
Overall dimensions Length: 36.100 mm Width: 24.250 mm Net height: 7.500 mm
TRANSPORT FEATURES
Maximum Load 10.000 kg
Board dimensions 1400x1100x50 mm
Block maximum height 500 mm
Deposit shelves 10
Board for shelf 1
Shelf distance 210 mm
Maximum weight block for shelf 500 kg
PRODUCTION FEATURES
Cycle Variable according to the type and quality of the manufactured product
Production per hour Variable according to the type and quality of the manufactured product
ENVIRONMENTAL CONDITIONS
Altitude on sea level Mt 1000 max
Working temperature 0 / +50°C
Electric part working temperature 5 / +35°C
Temperature with non-working machine -15 / +60°C
Max humidity 80%
UTILISATIONS
Electric (max 5% tension phase displacement) The electric board temperature must be included between +5/+40°C 400 V 50 Hz 3F + N + PE
Hydric Ø 1" at max pressure 3 bar
Pneumatic Ø 1/2" at max pressure 8 bar
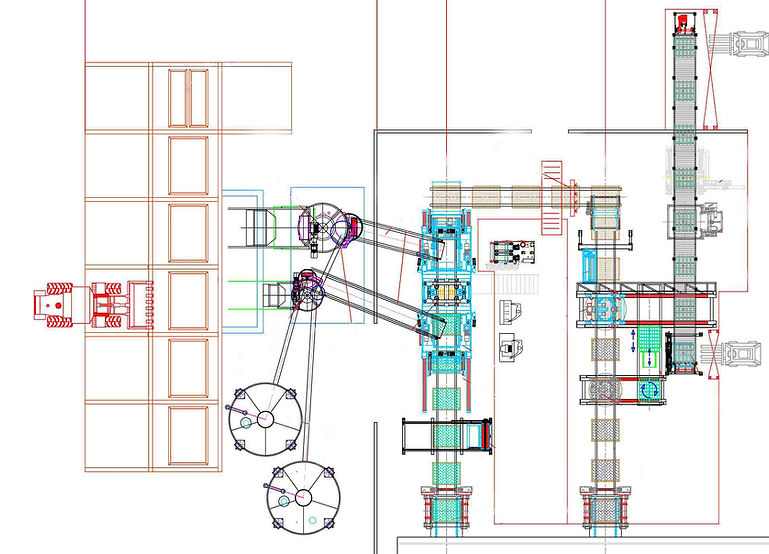
Block Machine
The main chassis is made of high-quality, arc-welded profiles that form a solid and robust base and are specially designed and dimensioned to accommodate all moving components involved in the production process. It features hardened and chrome-plated guide shafts for the tamper head chassis and mold handling system, ensuring durability and precision.
A sensor-controlled manual locking system is integrated to securely stabilize the tamper head chassis during maintenance work, ensuring safety and easy access.
Advance Servo Vibration
By enabling independent control of amplitude and frequency, the system allows vibration to be precisely tailored to specific molds and product requirements. This dual control capability ensures faster compaction and shorter finishing times compared to traditional vibrating systems. Additionally, vibration can be activated or deactivated multiple times within a single machine cycle, providing enhanced flexibility and efficiency
Pallet Scraper
Material build-up on pallets is automatically cleared during each machine cycle, ensuring consistent performance. The scraper blade's downward tension is fully adjustable, allowing it to be tailored to specific cleaning requirements for optimal efficiency.
Mold Insertion System
The Mold Insertion Device significantly simplifies and accelerates the mold change process. Powered by a pneumatic mechanism, it effortlessly lifts and lowers the entire mold assembly onto or off the mold tamper. The design allows the mold assembly to be manually rolled into or out of the mold tamper area, ensuring a seamless and efficient operation with minimal downtime.
Hydraulic System
The hydraulic system is meticulously designed for maximum performance, reliability, and precision. It comprises each engineered to meet the demanding requirements of high-efficiency manufacturing processes.
Advanced control hydraulic unit equipped with proportional valves, strategically mounted on board to minimize response time for control adjustments. Integrated feeding and oil-draining collectors for seamless hydraulic unit operation.High-pressure connections between the oil-pressure collectors, hydraulic units, and cylinders, using a combination of rigid and flexible pipes for durability and efficiency.
Tank Capacity: 1300 liters, ensuring sufficient oil supply for continuous operation.
Heat Exchanger: Coupled with an oil recirculation pump to maintain optimal temperature and prevent overheating.
Pressure Accumulators: For consistent and reliable system performance.
Variable-Capacity Piston Motor Pump Units: Delivering adjustable hydraulic flow for precise control.
Oil Heating Resistances: To ensure consistent viscosity in colder conditions.
Filters: High-efficiency delivery and drain filters with electronic blockage monitoring for proactive maintenance.
Inspection Manhole: Facilitating easy access for routine checks and maintenance.
Monitoring Systems: Includes level controls, safety thermostats, pressure control transducers, and precision manometers for comprehensive system oversight.
Vibration Table Bearings Lubrication Control Station
Tank Capacity: 200 liters, dedicated to the lubrication system.
Heat Exchanger: Paired with an oil recirculation pump for temperature control.
Inverter-Driven Motor Pump Unit: Ensures constant lubrication oil pressure, critical for smooth bearing operation.
Oil Heating Resistances: Maintain optimal oil conditions in varying temperatures.
Filters: Delivery and drain filters equipped with electronic blockage controls for uninterrupted operation.
Inspection Manhole: Simplifies access for maintenance tasks.
Monitoring Systems: Comprehensive level controls, safety thermostats, pressure control transducers, and manometers to ensure consistent and reliable operation.
This advanced hydraulic system delivers precision, reliability, and durability, meeting the most stringent requirements of modern manufacturing environments.
Photo_products | Dimensions (mm) | Description | Capacity per Palette(pcs) | Capacity per Day(pcs/8h) | Capacity per Day(pcs/8h) |
---|---|---|---|---|---|
162*198*60 | Behaton Paving Stone | 42 | 76800 | 76800 | |
160*196*80 | Paver Double T | 42 | 69000 | 69000 | |
200*100*80 | Paving Stone | 72 | 103000 | 103000 | |
90*190*390 | Block | 66 | 55000 | 55000 | |
140*190*390 | Block | 56 | 35000 | 35000 | |
190*190*390 | Block | 36 | 25000 | 25000 | |
150*250*1000 | Curbstone | 8 | 11520 | 11520 |

PRS 3000
Board dimensions 1400x1300 mm
DIMENSIONAL FEATURES
Overall dimensions Length: 38.400 mm Width: 26.150 mm Net height: 7.500 mm
TRANSPORT FEATURES
Maximum Load 12.000 kg
Board dimensions 1400x1300x50 mm
Block maximum height 500 mm
Deposit shelves 10
Board for shelf 1
Shelf distance 210 mm
Maximum weight block for shelf 800 kg
PRODUCTION FEATURES
Cycle Variable according to the type and quality of the manufactured product
Production per hour Variable according to the type and quality of the manufactured product
ENVIRONMENTAL CONDITIONS
Altitude on sea level Mt 1000 max
Working temperature 0 / +50°C
Electric part working temperature 5 / +35°C
Temperature with non-working machine -15 / +60°C
Max humidity 80%
UTILISATIONS
Electric (max 5% tension phase displacement) The electric board temperature must be included between +5/+40°C 400 V 50 Hz 3F + N + PE
Hydric Ø 1" at max pressure 3 bar
Pneumatic Ø 1/2" at max pressure 8 bar



Block Machine
The main chassis is made of high-quality, arc-welded profiles that form a solid and robust base and are specially designed and dimensioned to accommodate all moving components involved in the production process. It features hardened and chrome-plated guide shafts for the tamper head chassis and mold handling system, ensuring durability and precision.
A sensor-controlled manual locking system is integrated to securely stabilize the tamper head chassis during maintenance work, ensuring safety and easy access.
Pressure Tamper Control
The system operates with two oil-pressure cylinders, managed by a proportional valve and position-controlled through a linear encoder for precise and reliable operation. Each cylinder is equipped with bidirectional arrest devices, ensuring secure stem locking during emergency stops or maintenance tasks for maximum safety.
The tamper head is mounted to the chassis via a pneumatic mechanism and is isolated from the main structure using advanced anti-vibration elements. This design ensures stability and minimizes structural stress. Two electric vibration motors are installed on the upper section of the tamper head door to deliver controlled vibrations during the molding phase. These motors can be selectively activated or deactivated according to the production “recipe,” enhancing surface smoothness as needed.
The PRO 1411’s advanced quality control system includes pressure tamper control, which governs the tamper head movement during the molding phase. This feature is fully adjustable through recipe settings, enabling optimal performance across a wide range of products.
A user-friendly monitor interface allows operators to set the desired product height and define the maximum permissible variation tolerance. Any deviations are promptly signaled through an alarm notification on the display, ensuring precise production standards and effective quality management.
Mold Locking System
The mold movement and locking system are engineered for unmatched precision, stability, and efficiency, ensuring seamless integration into the production process. At its core is a robust mold-holding structure powered by two oil-pressure cylinders, meticulously controlled by a proportional valve and a high-precision linear encoder, delivering unparalleled accuracy in positioning.
A sophisticated pneumatic locking mechanism secures the mold onto advanced rubber anti-vibration elements, effectively isolating vibrations and maintaining exceptional stability throughout the mold-holder chassis's movement.
Once the mold is precisely positioned on the board, the locking system disengages with flawless precision, seamlessly releasing the mold from the holder. The vibration table, fully isolated from the machine’s structure, then presses the mold onto the board with controlled force, ensuring uniform compression. This innovative design not only guarantees superior product quality but also enhances operational reliability, making the system a cornerstone of high-performance manufacturing.
Hydraulic System
The hydraulic system is meticulously designed for maximum performance, reliability, and precision. It comprises each engineered to meet the demanding requirements of high-efficiency manufacturing processes.
Advanced control hydraulic unit equipped with proportional valves, strategically mounted on board to minimize response time for control adjustments. Integrated feeding and oil-draining collectors for seamless hydraulic unit operation.
High-pressure connections between the oil-pressure collectors, hydraulic units, and cylinders, using a combination of rigid and flexible pipes for durability and efficiency.
Tank Capacity: 1300 liters, ensuring sufficient oil supply for continuous operation.
Heat Exchanger: Coupled with an oil recirculation pump to maintain optimal temperature and prevent overheating.
Pressure Accumulators: For consistent and reliable system performance.
Variable-Capacity Piston Motor Pump Units: Delivering adjustable hydraulic flow for precise control.
Oil Heating Resistances: To ensure consistent viscosity in colder conditions.
Filters: High-efficiency delivery and drain filters with electronic blockage monitoring for proactive maintenance.
Inspection Manhole: Facilitating easy access for routine checks and maintenance.
Monitoring Systems: Includes level controls, safety thermostats, pressure control transducers, and precision manometers for comprehensive system oversight.
Vibration Table Bearings Lubrication Control Station
Tank Capacity: 200 liters, dedicated to the lubrication system.
Heat Exchanger: Paired with an oil recirculation pump for temperature control.
Inverter-Driven Motor Pump Unit: Ensures constant lubrication oil pressure, critical for smooth bearing operation.
Oil Heating Resistances: Maintain optimal oil conditions in varying temperatures.
Filters: Delivery and drain filters equipped with electronic blockage controls for uninterrupted operation.
Inspection Manhole: Simplifies access for maintenance tasks.
Monitoring Systems: Comprehensive level controls, safety thermostats, pressure control transducers, and manometers to ensure consistent and reliable operation.
This advanced hydraulic system delivers precision, reliability, and durability, meeting the most stringent requirements of modern manufacturing environments.
Robotic System (Stacking Robot)
Revolutionizing Concrete Block Production with Robotic Technologies
Robotic technologies play a critical role in concrete block production, speeding up production cycles, standardizing quality, and enhancing labor efficiency. Fully automated concrete block machines optimize the production process from start to finish, providing significant advantages in the following areas:
-
Molding and Filling Process:
Concrete mixtures are poured into high-precision mold using robotic systems, ensuring each product meets the same dimensions and desired strength. For example, machines offered by Auto Block Machine combine vibration and hydraulic pressing features, producing more compact and higher-strength blocks. These technologies enable the production of durable products ideal for heavy-duty projects. -
Handling and Stacking:
Robotic handling systems allow concrete blocks to be moved quickly and securely. Handbot modules automate the stacking of products in various sizes. These systems can be easily integrated into new production lines or used independently in existing facilities. -
Reducing Error Rates:
Robotic solutions minimize human errors, ensuring consistency in molding processes, which guarantees the production of standardized products. This enables cost-efficient production of high-quality concrete blocks. -
Sustainability and Energy Efficiency:
Robotic technologies that prioritize energy efficiency reduce energy consumption during production, lowering environmental impact. Manufacturers like Pres Makina specialize in developing long-lasting, environmentally friendly systems.
Robotic solutions combine economic and environmental benefits, transforming the concrete block production process. For more detailed
information, you can visit the websites of the relevant manufacturers:
ABM Curing System
Every system designed by ABM is engineered for precise control of temperature, humidity, and timing within the curing environment. Our systems ensure optimal insulation, air circulation, and energy efficiency to meet your requirements.
Using advanced custom simulation software, we tailor each curing system to align perfectly with your operational needs. Our skilled technical service team carries out installation and also provides on-site training to ensure your staff can operate the system at maximum efficiency.
ABM offers 24/7 technical support, spare parts, and comprehensive training services. Additionally, we provide upgrade options for ABM and competitive curing systems, ensuring your equipment remains state-of-the-art.
Finger Car Systems
Finger car systems used in automatic block machines are designed to efficiently and precisely handle the transportation and stacking of molded products during the production process. These systems transfer products along with pallets to curing or drying areas and position them as required.
With high load capacity, minimal energy consumption, and low maintenance requirements, finger car systems enhance efficiency in production lines. Additionally, full automation reduces labor needs, ensuring more reliable and controlled operations.
Photo_products | Dimensions (mm) | Description | Capacity per Palette(pcs) | Capacity per Day(pcs/8h) | Capacity per Day(pcs/8h) |
---|---|---|---|---|---|
162*198*60 | Behaton Paving Stone | 42 | 76800 | 76800 | |
160*196*80 | Paver Double T | 42 | 69000 | 69000 | |
200*100*80 | Paving Stone | 72 | 103000 | 103000 | |
90*190*390 | Block | 66 | 55000 | 55000 | |
140*190*390 | Block | 56 | 35000 | 35000 | |
190*190*390 | Block | 36 | 25000 | 25000 | |
150*250*1000 | Curbstone | 8 | 11520 | 11520 |